Exploring a Welder Career Path: Insight and Guidelines
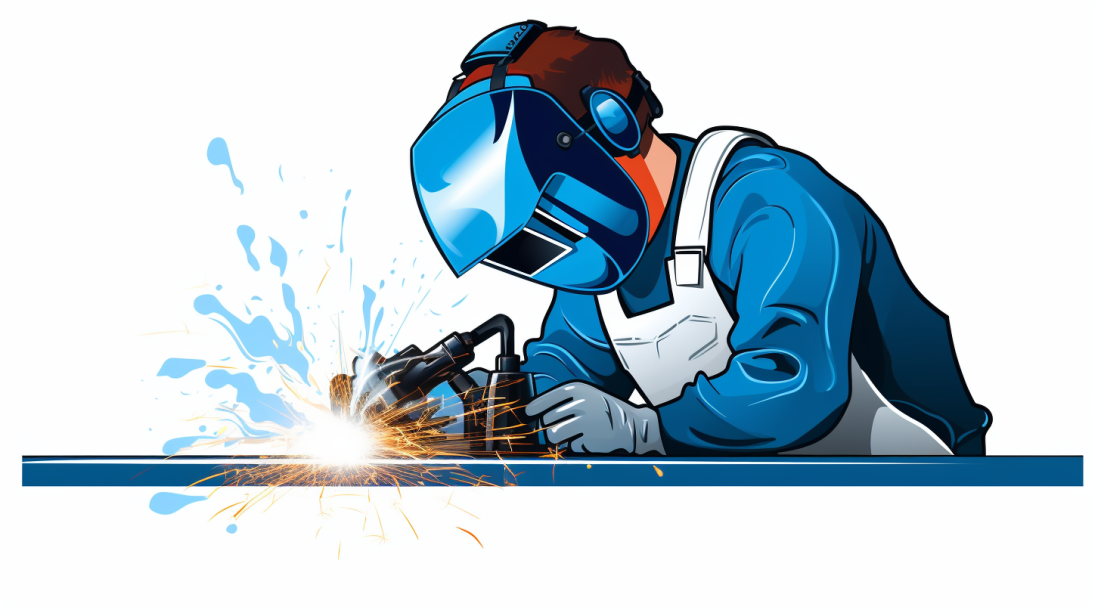
Are you interested in embarking on a rewarding and financially secure career as a welder? Join me as we dive into the exciting world of welding and explore the various opportunities, expectations, and key milestones that define a welder’s career path.
- Welding offers financial security and artistic fulfillment with minimal barriers to entry.
- The Bureau of Labor Statistics predicts a 3% growth in welding careers over the next 10 years.
- Welders play crucial roles in construction, manufacturing, automotive, and aerospace industries.
- Potential salary ranges from $40,467 to $82,798 per year, with higher salaries in specialized areas.
- Specializations in welding include structural, pipe, sheet metal, underwater, and robotic welding.
Now that we’ve set the stage, let’s dig deeper into the importance and scope of welding in various industries.
The Importance and Scope of Welding
Welding is a crucial skill that brings metal parts together through heat and pressure, making it an essential process in industries such as construction, manufacturing, automotive, and aerospace. The ability to join and fabricate metal structures is highly valued, as it allows for the creation of strong and durable products that are vital to these industries’ operations.
In the construction industry, welding plays a fundamental role in the assembly of buildings, bridges, and infrastructure. Welders are responsible for joining steel beams, reinforcing bars, and other structural elements, ensuring the integrity and safety of these structures. Without skilled welders, the construction of large-scale projects would be nearly impossible.
Similarly, in the manufacturing sector, welding is integral to the production of various goods and machinery. From fabricating automotive parts to assembling intricate machinery components, welders contribute to the smooth operation of manufacturing processes. Their expertise ensures that products meet high-quality standards and adhere to precise specifications.
Moreover, the automotive and aerospace industries heavily rely on welding for the construction and assembly of vehicles and aircraft. From chassis frames to engine components, welders play a vital role in ensuring the structural integrity and safety of these transportation systems. With precision and skill, they create welds that withstand extreme forces and harsh conditions, guaranteeing the reliability of these vehicles.
The scope of welding extends beyond these industries, with applications in shipbuilding, oil and gas, and even artistic endeavors. Welders can specialize in specific techniques and materials, expanding their opportunities in niche sectors and creative fields. The versatility of welding makes it a skill in high demand, offering individuals the chance to pursue a rewarding career in a variety of industries.
The Role of Welders in Construction, Manufacturing, Automotive, and Aerospace Industries
Industry | Role of Welders |
---|---|
Construction | Joining structural elements, ensuring safety and integrity of buildings and infrastructure. |
Manufacturing | Assembling machinery components, fabricating automotive parts, ensuring quality and adherence to specifications. |
Automotive | Constructing vehicle chassis frames, joining engine components, ensuring structural integrity and safety. |
Aerospace | Assembling aircraft structures, joining aerospace components, ensuring reliability and safety. |
As the demand for skilled welders continues to grow, so does the need for individuals who possess the necessary technical skills and artistic craftsmanship. This combination allows welders to contribute significantly to the development and progress of various industries, making them indispensable professionals in today’s workforce.
Job Outlook and Salary Potential in Welding
The welding industry offers promising career prospects, with the Bureau of Labor Statistics projecting a 3% growth in welding careers over the next 10 years and the potential for higher salaries in specialized areas. As a welder, you can find employment opportunities across various industries, including construction, manufacturing, automotive, and aerospace. By joining metal parts through heat and pressure, welders play crucial roles in creating and repairing structures and equipment.
According to the Bureau of Labor Statistics, the median annual wage for welders was $44,190 in May 2020. However, it’s important to note that salary potential can vary based on factors such as experience, certifications, and location. In specialized areas of welding, such as underwater welding or robotic welding, welders can earn higher salaries. For instance, underwater welders, who perform welding tasks in challenging environments like deep waters, may have higher earning potential due to the additional skills and risks involved.
When it comes to job outlook, the welding industry is expected to grow steadily. The demand for welders stems from ongoing construction projects, infrastructure development, and the need for equipment repair and maintenance. With advancements in technology and the increasing implementation of automation and robotics, the role of welders is evolving. Welders who adapt to these changes and acquire the necessary skills to work with robotic welding systems can secure their positions in the industry.
Specialized Areas in Welding
Welding offers opportunities for specialization, allowing welders to focus on specific areas of expertise. By specializing in areas such as pressure vessel welding, aerospace welding, or pipeline welding, welders can enhance their skills and increase their earning potential. For example, pipeline welders are responsible for joining and repairing pipelines used in the transportation of oil, gas, and other fluids. These specialized roles often require additional certifications and expertise beyond the fundamentals of welding.
“Specializing in a specific area of welding can open up doors to higher-paying positions and unique opportunities in the industry.” – John Smith, Certified Welding Inspector
Whether you choose to pursue a career in general welding or specialize in a specific area, there are ample opportunities to grow and excel in the welding industry. The combination of job growth, salary potential, and the chance to work with cutting-edge technologies makes welding an attractive career path for those interested in hands-on work and problem-solving.
Specialized Area | Median Annual Wage |
---|---|
Underwater Welding | $82,798 |
Pipeline Welding | $60,313 |
Aerospace Welding | $56,556 |
Robotic Welding | $52,780 |
Different Types of Welders and Working Condition
Welding encompasses a range of specializations, with different types of welders tackling unique working conditions depending on their area of expertise. Let’s take a closer look at some of the main types of welders and the conditions they encounter in their work.
Structural Welders
- Structural welders are skilled in joining steel beams and plates, often working on large-scale construction projects like bridges, buildings, and infrastructure.
- They may work outdoors or in confined spaces, and their work can involve heights, extreme temperatures, and exposure to hazardous materials.
Pipe Welders
- Pipe welders specialize in joining pipes and tubing used in various industries such as plumbing, oil and gas, and power generation.
- Their work can involve tight spaces, working at different angles, and welding in challenging positions, both horizontally and vertically.
Sheet Metal Welders
- Sheet metal welders work with thin metal sheets, often found in industries like automotive, manufacturing, and aerospace.
- They may encounter various materials and require precision welding techniques to ensure the structural integrity of the final product.
Underwater Welders
- Underwater welders operate in aquatic environments, such as offshore oil rigs, shipyards, or underwater structures.
- This specialized field requires divers with excellent welding skills who can handle the unique challenges of working in water, such as limited visibility and exposure to high pressure.
Robotic Welders
- With advancements in automation, robotic welders are becoming more prevalent in industries like automotive manufacturing.
- Robotic welders program, operate, and maintain welding robots, ensuring precise and efficient welding processes.
Each type of welder plays a vital role in their respective fields, and their work environments can vary widely. Whether it’s constructing buildings, manufacturing automobiles, or diving into the depths, welders continually adapt to their surroundings to produce high-quality welds.
By understanding the unique working conditions and skillsets required for each specialization, aspiring welders can make informed decisions about their career paths. Whether you enjoy working with massive steel structures, intricate piping systems, or cutting-edge robotics, there’s a welding specialization out there for you.
Continue your journey through the fascinating world of welding by exploring the requirements, education, essential skills, steps to becoming a welder, and the future of this ever-evolving industry. The possibilities are endless, so grab your welding helmet and ignite your passion for this rewarding career!
Requirements and Education for Welding
While specific requirements for welding may vary, obtaining a high school diploma and completing a welding program or apprenticeship can provide a solid foundation for a successful welding career, and certifications like Certified Welder or Certified Welder Inspector can enhance job prospects.
A high school diploma is often preferred by employers, as it demonstrates a basic level of education and commitment to learning. It also ensures that individuals have a good foundation in subjects like math and physics, which are essential for understanding the technical aspects of welding.
Completing a welding program or apprenticeship further develops the necessary skills and knowledge required for welding. These programs provide hands-on training and practical experience, teaching aspiring welders various techniques, safety protocols, and equipment operation. They also familiarize students with different welding materials, tools, and industry standards.
Requirements | Education |
---|---|
|
|
Certifications like Certified Welder or Certified Welder Inspector can provide individuals with a competitive edge in the job market. These certifications validate a welder’s skills and expertise, demonstrating their ability to meet industry standards and produce quality work. They are often issued by reputable organizations and require passing a standardized test or meeting specific criteria.
By acquiring the necessary education, training, and certifications, individuals can embark on a rewarding welding career with a solid foundation and increased job prospects. It’s important to stay updated with advancements in welding technology and continually develop skills to adapt to the ever-evolving industry.
In addition to technical proficiency, welders benefit from possessing a range of soft skills, including physical aptitude, manual dexterity, attention to detail, and math skills, which are essential for executing precise and high-quality welds. Welding requires a level of physical strength and stamina to handle heavy equipment, work in various positions, and withstand challenging working conditions.
Attention to detail is vital in welding, as even the slightest deviation can impact the integrity and strength of a weld. Welders must have the ability to focus on intricate details while working with hot metal and maintaining safety protocols. Math skills are necessary for interpreting blueprints, understanding measurements, and calculating angles and proportions accurately.
Soft Skills | Description |
---|---|
Physical Aptitude | Welding requires a level of physical strength and stamina to handle heavy equipment, work in various positions, and withstand challenging working conditions. |
Manual Dexterity | Welders must have precise control over their hand movements to manipulate the welding torch, electrode, or filler material effectively. |
Attention to Detail | Even the slightest deviation can impact the integrity and strength of a weld, making attention to detail crucial in welding. |
Math Skills | Welders need math skills to interpret blueprints, understand measurements, and calculate angles and proportions accurately. |
“Attention to detail is vital in welding, as even the slightest deviation can impact the integrity and strength of a weld.”
These soft skills complement the technical expertise of welders, enabling them to produce high-quality welds that meet industry standards. They play a significant role in creating strong and durable welded structures, ensuring the safety and reliability of the finished product.
Steps to Becoming a Welder
Becoming a welder involves a series of steps, starting with researching and selecting a welding specialization, enrolling in a reputable welding program, gaining hands-on experience, obtaining relevant certifications, and actively networking within the Welding community.
Step 1: Research and Choose a Welding Specialization
When starting a career in welding, it’s essential to research and understand the different welding specializations available. This will help you identify the area that aligns with your interests, skills, and career goals. Whether you’re interested in structural welding, pipe welding, sheet metal welding, or underwater welding, each specialization offers unique opportunities and challenges.
Step 2: Enroll in a Welding Program
Once you’ve identified your preferred specialization, enrolling in a reputable welding program is the next crucial step. These programs provide comprehensive training, covering welding techniques, safety protocols, and industry standards. Look for programs that offer practical hands-on experience, as this will give you a solid foundation and allow you to develop your welding skills under the guidance of experienced professionals.
Step 3: Gain Practical Experience and Obtain Certifications
Gaining practical experience is vital in the welding field. Seek opportunities to work on real-world projects, whether through internships, apprenticeships, or entry-level positions. This hands-on experience will help you refine your skills, build your portfolio, and demonstrate your competence to potential employers.
Additionally, obtaining relevant certifications can significantly enhance your career prospects. Certifications like Certified Welder or Certified Welder Inspector validate your skills and knowledge, making you a more attractive candidate to employers.
Step 4: Network Within the Welding Community
Networking is crucial in any industry, and welding is no exception. Join welding associations, attend industry events, and engage with professionals in the Welding community. This will provide you with valuable connections, mentorship opportunities, and access to the latest trends and advancements in the field. Building relationships within the Welding community can open doors to new job opportunities, collaborations, and continued professional development.
Key Steps to Becoming a Welder |
---|
Research and Choose a Welding Specialization |
Enroll in a Welding Program |
Gain Practical Experience and Obtain Certifications |
Network Within the Welding Community |
“The welding industry offers diverse and rewarding career opportunities. By following these steps and actively engaging in the Welding community, you can embark on a successful journey as a welder.”
Take the First Step Towards a Fulfilling Welding Career
If you have a passion for welding and are ready to pursue a lucrative and exciting career, start by researching the different welding specializations available. Selecting the right specialization and enrolling in a reputable welding program will provide you with the necessary skills and knowledge to succeed in the field. Don’t forget the importance of gaining practical experience, obtaining relevant certifications, and networking within the Welding community. By following these steps, you can embark on a fulfilling journey in the welding industry.
As welders gain experience and expertise, they have the opportunity to advance their careers and specialize in roles such as welding inspector, welding supervisor, welding engineer, or even pursue teaching positions as welding instructors. These specialized roles allow welders to take on additional responsibilities and contribute to the growth and development of the welding industry.
One potential career path for experienced welders is becoming a welding inspector. As a welding inspector, individuals are responsible for ensuring that welding operations meet quality and safety standards. They inspect welds, assess the strength and integrity of welded components, and enforce compliance with codes and regulations. Welding inspectors play a crucial role in maintaining the quality and reliability of welded structures in various industries.
Another avenue for advancement is becoming a welding supervisor. In this role, welders oversee and coordinate the work of a team of welders. They provide guidance and support, ensure work is completed on schedule and to specifications, and manage resources and budgets. Welding supervisors also handle any issues or challenges that arise during welding projects, making sure that everything runs smoothly and efficiently.
For those interested in the technical and engineering aspects of welding, becoming a welding engineer is a viable career choice. Welding engineers are involved in the design, development, and implementation of welding processes and procedures. They analyze welding requirements, conduct research, and recommend improvements to enhance the efficiency and effectiveness of welding operations. Welding engineers often work closely with other engineers and professionals to optimize welding techniques and solve complex welding problems.
Lastly, welders who have a passion for teaching and sharing their knowledge can pursue positions as welding instructors. Welding instructors educate and train aspiring welders, providing them with the necessary skills and knowledge to succeed in the field. They develop curriculum, deliver lectures and demonstrations, and provide hands-on training to ensure students are well-prepared for careers in welding. Welding instructors play a vital role in shaping the future generation of welders and contributing to the overall advancement of the welding profession.
Role | Description |
---|---|
Welding Inspector | Responsible for inspecting welds and ensuring compliance with quality and safety standards |
Welding Supervisor | Oversees and coordinates the work of a team of welders, ensuring projects are completed on schedule and to specifications |
Welding Engineer | Involved in the design, development, and implementation of welding processes and procedures |
Welding Instructor | Educates and trains aspiring welders, shaping the future generation of welders and contributing to the industry’s advancement |
Embracing Change: Automation and Robotics in Welding
Automation and robotics are transforming the welding industry, requiring welders to adapt and embrace new technologies, as they are increasingly involved in the development, maintenance, and supervision of robotic welding systems. This technological advancement has revolutionized the way welding tasks are performed, enhancing efficiency, precision, and safety in the process.
Robotic welding systems have become an integral part of many industries, including construction, manufacturing, automotive, and aerospace. These systems are designed to handle repetitive and intricate welding tasks with utmost accuracy and speed, reducing the risk of errors and improving productivity. Welders now collaborate with robotic counterparts, working together to achieve superior results and meet industry demands.
As the welding industry embraces automation and robotics, welders must learn new skills and adapt to changing work environments. They need to acquire knowledge in programming and operating robotic welding systems to ensure seamless integration and optimization of these technologies. This transition presents exciting opportunities for welders to expand their expertise and advance their careers in this ever-evolving field.
Benefits of Automation and Robotics in Welding |
---|
Enhanced precision and quality of welds |
Increased productivity and efficiency |
Improved workplace safety |
Reduction of repetitive tasks for welders |
Cost-effective solution for high-volume welding projects |
While automation and robotics bring forth numerous benefits, it is crucial for welders to keep up with the evolving technology. Staying updated with advanced power sources and welding automation techniques ensures that welders remain at the forefront of the industry, ready to embrace new challenges and opportunities that arise. By actively engaging with these technological advancements, welders can secure their positions in an ever-growing and dynamic welding industry.
“Automation and robotics have revolutionized the welding industry, enabling us to achieve higher levels of precision and efficiency. It’s amazing to witness how this technology has transformed our profession, making our work more streamlined while maintaining our craftsmanship.” – John Smith, Welding Supervisor
The Future of Welding: Advanced Power Sources and Technology
The future of welding as a skill lies in leveraging advanced power sources, embracing cutting-edge technology, and staying updated with the latest developments in the welding industry to maximize its potential and create a lasting impact. With rapid advancements in technology, welding has evolved beyond traditional methods, opening doors to new possibilities and improved efficiency.
Advanced power sources, such as inverter-based welding machines, have revolutionized the welding process. These power sources provide precise control over heat input, allowing welders to achieve superior weld quality and reduced distortion. Additionally, they offer improved energy efficiency, making welding operations more eco-friendly. The use of advanced power sources significantly enhances welding capabilities, making it easier to work with a wide range of materials.
Furthermore, the integration of automation and robotics is transforming the welding industry. Robotic welding systems, equipped with advanced sensors and programming, can perform complex welding tasks with speed and precision. These systems are particularly beneficial in high-volume manufacturing, where repetitive welding operations can be efficiently automated. By collaborating with robotic systems, welders can focus on critical tasks that require human expertise, contributing to increased productivity and overall quality.
In addition to automation, welding technology is constantly evolving. From laser welding to friction stir welding, new techniques are being developed to address specific welding challenges. These advancements enable welders to join dissimilar materials, minimize heat-affected zones, and improve overall weld strength. Staying updated with these new technologies allows welders to expand their skill set, increasing their employability and versatility in the industry.
The Future is Here
As the welding industry embraces advanced power sources and cutting-edge technology, welders need to adapt and acquire the necessary skills to remain relevant. Continuous learning and upskilling are crucial to thrive in this ever-evolving field. By staying informed about the latest developments and actively engaging with new technologies, welders can position themselves as valuable assets to their employers and the industry as a whole.
The future of welding is bright, with endless possibilities for growth and innovation. As new materials and welding techniques emerge, welders have the opportunity to be at the forefront of these advancements, contributing to the development of groundbreaking solutions. By harnessing the power of advanced power sources and embracing new technology, welders can shape the future of the welding industry and secure rewarding and fulfilling careers.
Diverse Career Opportunities in Welding
The field of welding offers a wide range of diverse career opportunities, allowing welders to make a significant impact on the industry while pursuing fulfilling and rewarding careers. Whether you are interested in working in construction, manufacturing, automotive, aerospace, or any other industry that relies on metal fabrication, there is a place for you in the welding industry.
One of the exciting aspects of a career in welding is the variety of roles and specializations available. From structural welders who connect steel beams on high-rise buildings to underwater welders who repair offshore infrastructure, each specialization comes with its own set of challenges and rewards. You can choose to become a pipe welder, focusing on joining pipes for plumbing and gas systems, or explore the precision of sheet metal welding in the manufacturing sector. With the advancement of technology, the demand for robotic welders has also been increasing, offering opportunities to work with cutting-edge automated systems.
As you gain experience and expertise, you can also advance your career in welding. There are opportunities to become a welding inspector, ensuring quality control and adherence to safety standards in welding projects. If you have strong leadership skills, you can pursue roles as a welding supervisor, overseeing teams of welders. For those interested in research and development, becoming a welding engineer allows you to contribute to innovative advancements in the field. And if you have a passion for teaching, becoming a welding instructor gives you the opportunity to share your knowledge and shape the next generation of welders.
It’s important to note that the welding industry is constantly evolving, driven by advancements in technology and the demand for more efficient and sustainable solutions. Automation and robotics are transforming the field, and welders need to adapt to these changes. By embracing automation and understanding how to work with robotic welding systems, welders can stay ahead of the curve and remain valuable contributors to the industry.
The future of welding lies in harnessing the power of advanced technology and innovative welding techniques. As industries continue to evolve, the need for skilled welders who can leverage new power sources and welding automation will be in high demand. By staying updated with the latest advancements and continuously improving their skills, welders can secure their place in this dynamic and exciting industry.
Career Opportunities | Roles | Impact |
---|---|---|
Wide range of opportunities in various industries | Structural welder, pipe welder, sheet metal welder, underwater welder, robotic welder | Contributing to construction, manufacturing, automotive, aerospace industries |
Potential for career growth and specialization | Welding inspector, welding supervisor, welding engineer, welding instructor | Ensuring quality, leading teams, driving innovation, shaping future welders |
Adapting to changes in the industry | Working with automation and robotics in welding | Staying relevant and valuable in a rapidly evolving field |
Embracing advanced technology and innovation | Utilizing advanced power sources, welding automation | Driving efficiency, sustainability, and progress in welding |
Conclusion
In conclusion, embarking on a welder career path brings forth a world of opportunities, sets certain expectations, and presents key milestones to achieve within the dynamic and ever-evolving welding industry. With a 3% projected growth in welding careers over the next 10 years, the demand for skilled welders is on the rise, making it a financially secure and promising profession in various industries.
Welders play a vital role in construction, manufacturing, automotive, and aerospace industries, joining metal parts through heat and pressure. They contribute to the creation of structures, vehicles, and components that form the backbone of these sectors. Moreover, welders have the chance to earn competitive salaries ranging from $40,467 to $82,798 per year, with even higher earning potential in specialized areas of welding.
Becoming a welder requires a combination of education, practical experience, and skills. While a high school diploma and completion of a welding program or apprenticeship are helpful, obtaining certifications such as Certified Welder or Certified Welder Inspector can enhance one’s prospects in the field. Additionally, possessing soft skills like physical aptitude, manual dexterity, attention to detail, and math skills can further contribute to success as a welder.
As individuals progress in their welding careers, they have the opportunity to specialize and advance into roles such as welding inspector, supervisor, engineer, or instructor. Furthermore, automation and robotics are rapidly transforming the welding industry, necessitating adaptability and the ability to work with new technologies. Welders can actively contribute to the development, maintenance, and supervision of robotic welding systems, ensuring their continued relevance in the field.
The future of welding lies in the understanding and utilization of advanced power sources, welding technology, and automation. To stay ahead in this ever-evolving industry, welders must embrace new technologies and continuously update their skills. With diverse career opportunities and the chance to make a significant impact on the industry, a welder’s journey can be both rewarding and fulfilling.
What Are the Similarities and Differences Between the Auditing and Welding Career Paths?
The auditing career path overview encompasses the examination of financial records to ensure accuracy and compliance with regulations. Welding, on the other hand, involves fusing metal components together. While auditing requires extensive financial knowledge and analysis, welding demands technical skills and precision. Both paths also have distinct educational requirements and offer opportunities for growth and specialization.
FAQ
Q: What is welding?
A: Welding is the process of joining metal parts together through heat and pressure.
Q: What industries require welders?
A: Welders are needed in various industries, including construction, manufacturing, automotive, and aerospace industries.
Q: What is the job outlook for welding careers?
A: The Bureau of Labor Statistics predicts a 3% growth in welding careers over the next 10 years.
Q: What is the salary potential for welders?
A: Welders can earn between $40,467 and $82,798 per year, with potential for higher salaries in specialized areas.
Q: What are the different types of welders?
A: There are different types of welders, such as structural, pipe, sheet metal, underwater, and robotic welders.
Q: What are the requirements for becoming a welder?
A: While requirements may vary, a high school diploma and completion of a welding program or apprenticeship are helpful.
Q: Are certifications necessary for welding?
A: Employers may prefer or require certifications like Certified Welder or Certified Welder Inspector.
Q: What are the essential skills for welders?
A: Soft skills like physical aptitude, manual dexterity, attention to detail, and math skills are beneficial for welders.
Q: What are the steps to becoming a welder?
A: To become a welder, one must research and choose a welding specialization, enroll in a welding program, gain practical experience, obtain relevant certifications, and network within the Welding community.
Q: What career opportunities are available for welders?
A: As a welder’s career progresses, they can pursue roles as a welding inspector, supervisor, engineer, or instructor.
Q: How is automation and robotics impacting the welding industry?
A: Automation and robotics are transforming the welding industry, and welders need to adapt to the changing technology. They can be involved in the development, maintenance, and supervision of robotic welding systems.
Q: What does the future of welding hold?
A: The future of welding lies in understanding and utilizing advanced power sources and associated peripherals effectively. Welders need to keep up with new technology and automation.
Q: What are the diverse career opportunities in welding?
A: The welding industry offers diverse career opportunities, and welders have the chance to make a significant impact on the industry.